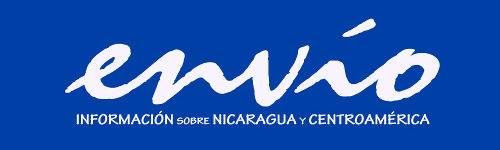
International
Clean Up Your Computer
CAFOD investigated electronics assembly plants in Mexico and China
to learn first hand how they work and how their workers live.
This text summarizes that important initiative,
which concludes that our computers are very “dirty.”
The Catholic Agency for Overseas Development (CAFOD)
Computers are an integral part of everyday life. Thirty years ago, it would have been hard to imagine their centrality in everyday life. Now, it’s hard to imagine life without them. Computers are not only ubiquitous; they are also well on the way to becoming disposable. With a constant stream of slimmer, lighter, faster models emerging on the market, they are no longer a long-term investment for the buyer, as they were ten or even five years ago. But while the number of computers being sold keeps growing, the dollar size of the market is static. In other words, consumers are buying many more computers than they used to, but they are paying much less for them.
Nowadays, many people make a connection between the clothes they buy and the workers who make them. Consumers have some idea of the long hours of toil and discomfort behind the labels “Made in Bangladesh” or “Made in China”. The working conditions of the people who make computers and their components are not yet so well known, but they are in many respects similar.
The 138,468,000 personal computers that left the computer factories around the world in 2003 were not produced in some Silicon Valley utopia. Much of the manufacturing of desktop and laptop PCs and the peripheral devices such as printers, monitors and mice commonly used with them is done in developing countries by poor people working in harsh conditions.
IBM, Hewlett Packard and Dell:
Big brands, big profitsThe term “personal computer” (PC) was first coined in 1975 in an advertising campaign for one of the earliest portable computers, the Altair. A personal computer is digital, automatic, programmable, accessible and relatively small, inexpensive and simple: in short, it consists of the central processing unit (CPU), monitor, keyboard and mouse with which most people today are familiar.
The availability of cheap personal computers has undoubtedly had positive effects. First, it has provided hundreds of thousands of jobs around the world. Second, easy access to computers in the North has provided various social goods, including better communication between communities, educational opportunities and increased efficiency.
Multinational personal computer companies are some of the biggest and most successful in the world. The largest computer companies are American and Japanese, and three US companies have the largest share of the PC market: Dell, with 17.6%; Hewlett Packard, with 16.1%; and IBM, with just under 7%. These companies are “original equipment manufacturers” (OEMs): they build their own products from components largely bought from other manufacturers.
IBM has been selling business machines since the beginning of the 20th century. It kept itself at the forefront of the computer revolution when it targeted the first business computers to a mass market in the 1960s. When it entered the personal computer market in the early 1980s, it soon set the gold standard in PCs and spawned a multitude of clones. After a recent difficult period, IBM turned profits of US$1.8 billion for the third quarter of 2003 from revenues of US$21.5 billion, up from US$1.3 billion for the same period in 2002.
Hewlett Packard (HP), one of the original Silicon Valley start-ups of the 1950s, completed the largest corporate merger ever in the information technology sector in April 2002, when it joined forces with rival Compaq, but a year later its PC division was in the red. It has traditionally positioned itself as a manufacturer of high quality products, so it remains to be seen how HP will compete with Dell’s high-volume, low-cost model.
Dell, incorporated in 1984, became the world’s number one seller of PCs in the first quarter of 2003, when it overtook rival Hewlett Packard. It has slashed its prices by selling directly to the customer, largely through the Internet, cutting out dealers and other intermediaries with their associated costs. Michael Dell started the company in his freshman dormitory at the University of Texas in Austin and is today the third highest-paid US CEO and the 24th richest person in the world, with an estimated wealth of well over US$16 billion. The company had revenues of US$31 billion in 2001.
The PC sector: A white-knuckle ride The computer business is intensely competitive and moves at high speed. As one analyst put it, “This industry is like traveling in a car at nearly 200 miles an hour and all you see is out of the back and side windows.” The sector is characterized by falling prices, rapid technological change, volatility and the absence of trade unions.
Falling prices. The price of computers has fallen dramatically in the past 20 years. The price of a PC fell by an average 27% a year from 1976 to 1999, and the rate of decrease accelerated throughout the 1990s. Recently, prices were pushed even lower by the success of Dell’s low-cost business model and aggressive price-cutting: Dell recently slashed the price of its cheapest PC by 22%. While Dell’s innovation has been to sell directly to the customer, all major companies have been able to cut prices by operating an efficient “just in time” inventory system, keeping only a few days’ supplies of components in their warehouses.
Technological change. The pace of technological change in the computer sector is hectic: the capacity of chips doubles every 18 to 24 months and computer processing power has increased by a factor of 100 over the past decade. Sociologist Manuel Castells estimates that the technological capacity of computers has grown faster than any other technology in human history. Competition between the transnational corporations focuses on the technological advantages they can offer customers, and product life cycles are short. Consumers buy only the latest technology and last year’s (and often last month’s) innovations sit abandoned on the shop floor. Computer systems also change quickly: old computers cannot run new programs. This technological dynamism places tremendous pressure on companies to develop, produce and sell new technology quickly, and to compete in providing customer support.
Volatility. Fast technology turnover and fluctuating market demand create enormous instability in the computer supply chain. Frequent crashes in demand for a product cause companies to lurch between periods of overproduction and surplus capacity. Dell hit a crisis in 1989 when chip capacity went from 256K to 1Mb practically overnight and the company was left with millions of dollars’ worth of unsaleable stock. As one Dell executive commented: “Inventory has the shelf life of lettuce.”
Absence of trade unions. Lack of unions is a general characteristic of the sector. In the US, the electronics industry has historically been one of the least organized. The words of Robert Noyce, co-founder of Intel, epitomize the industry’s attitude to trade unions: “Remaining non-union is an essential for survival for most of our companies. If we had the work rules that unionized companies have, we’d all go out of business.”
Outsourcing Because falling prices, volatility and the demands of research and development drive down revenues, companies look to their supply chains to provide the savings that allow them to stay profitable. Computer multinationals exert enormous pressure on their suppliers, in order to reduce the costs of making computers.
Until the 1990s, major computer companies manufactured most of their product “in house,” and the workers on the factory production lines were employees of those companies. Increasingly, however, companies outsource much of the manufacturing process: that is, they buy parts or services from external suppliers. Dell, while retaining some US facilities, has done this from early on in its history, and it is one factor behind its success. One estimate is that 73% of industry-wide production will be outsourced by 2004. The big brands retain some manufacturing function, but concentrate on what they have come to see as their core competencies: research and development, marketing, sales, customer services and brand management.
Outsourcing has two major benefits for the computer multinationals: lower costs and greater flexibility. OEMs reduce capital investment in production sites, and with it the risk of losing money should the site cease to be viable. Outsourcing is particularly good value when external companies have specialized skills and expertise. The money saved can be applied elsewhere—marketing and advertising, for example—to increase profit. Outsourcing to developing countries also reduces wage bills.
When they are not tied to production sites through property ownership and permanent staff contracts, OEMs can respond more quickly to market demands and slumps. If demand grows, they can commission a new production line; if demand slumps, they can simply close the line. Micromanagement of supply also reduces costly storage of large quantities of products. This flexibility is crucial, given the sector’s fluctuating demand and technological pace. In addition, it allows for fast relocation. If wages in one country rise, outsourcing makes it easier to move somewhere else, where costs are cheaper.
The most globalized industry on the planet IBM, Hewlett Packard and Dell outsource much of their manufacturing outside the United States, particularly in developing countries. Electronics was one of the first industries in which stages of the production process were outsourced to developing countries, facilitated by the ability to trade the computer’s component parts like commodities because they are increasingly standardized, easily replicable and cheap.
The electronics sector has been in the vanguard of the globalization of production processes and is now “the most globalized of all industries,” according to the UN Conference on Trade and Development (UNCTAD) 2002 report. More than a third of all electronics exports now come from developing countries. According to UNCTAD, electronics are also the fastest growing of all developing country exports. Between 1980 and 1998, the share of electronic products in developing country exports increased fourfold, from 5.3% to 22%.
Confounding popular preconceptions, high technology exports are now the largest foreign exchange earners for the developing world—worth $450 billion in 2000. Electronics exports are worth more than all developing country agricultural exports and nearly three times more than developing country textile exports.
This process started during the 1980s when Japanese companies, faced with appreciation of the yen and increased labor costs at home, moved production to Taiwan and Singapore. US companies followed suit and developed partnerships with Asian-based suppliers. The past two decades have seen this process increase in speed and volume. Japanese, US, Singaporean and Taiwanese companies have moved parts of their production process to lower-cost countries such as the Philippines, Malaysia and Thailand. Since then, even lower-cost countries (notably China) have emerged, precipitating another wave of relocation.
Outsourcing has had a major effect on a large cluster of developing countries in East Asia and a smaller number in Central and Latin America. Malaysia’s economy used to rely on palm oil and tin; now, 53% of its export earnings come from electronics equipment. South Korea’s main exports in the early 1960s were textiles, plywood and wigs made of human hair; by 2001, electronics dominated its exports. Costa Rica’s main exports, once bananas and coffee, are now computers and computer parts at 35% of its total exports. Electronics equipment was worth 13% of Indonesia’s total exports, 26% of Thailand’s and a huge 63% of The Philippines’ in 2000, while computers and computer parts made up 20% of Taiwan’s exports and semiconductors and computers made up more than 50% of Singapore’s in the same year. Electronics exports are now the largest single segment of Mexico’s export trade.
What stays in the exporting countries?Outsourcing is not, however, always beneficial for developing country economies. By a combination of historical factors and industrial policy, some, notably the mature Asian tigers (Singapore, South Korea and Taiwan), have been able to use export booms to upgrade facilities, increase competitiveness and achieve sustained growth. Others, however, have been less successful.
Many of the skills embodied in electronics exports are produced in technologically advanced developed countries, while developing countries engage mainly in the low-skill, low value-added assembly stages of the global production chain. Export expansion has not been accompanied by increases in value added or income earned in developing countries. Much of the value added contained in these products accrues to foreign owners of capital, knowledge and management. The benefit developing countries derive from entering such a market can decline when other, cheaper countries enter as well.
The outsourcing process goes hand in hand with relocation to low-wage economies. Wage rates have provided powerful incentives for companies looking for a “lower cost footprint” and a competitive advantage, but wages are not the only factor in deciding where to locate a computer factory. The companies also consider the skills and education level of the work force according to the product they want to manufacture; the country’s transport, energy distribution and communication services infrastructure; its political and economic stability; the incentives its government provides in tax and custom duty concessions; and the country’s distance from the key centers in the company’s supply chain, favoring countries that have preferential access to the Western markets.
Outsourcing to contract manufacturers Big computer brands have been supplanted in the production process by a new breed of “contract manufacturers.” These companies are invisible and anonymous to consumers but are very large and powerful. They have grown at phenomenal rates, averaging 20-25% a year during the 1990s. Barely existing at the beginning of the 1990s, the four largest contract manufacturers—Solectron, Flextronics, Samina-SCI and Celestica—each had revenues of over US$10 billion by 2002.
Flextronics, for example, started by “board stuffing” circuit boards in Silicon Valley during the 1980s and is now the second largest contract manufacturer in the world, with revenues of US$13.2 billion in 2002. Incorporated in Singapore with its management offices in San José, California, Flextronics has factories worldwide. Its industrial parks, which house suppliers on site, are concentrated in Brazil, China, Hungary and Mexico. Its workers are paid anywhere from US$0.70 an hour in China to US$4.50 in Brazil. Flextronics has 15 locations in China alone and exported US$0.5 billion worth of goods from there in 2000. Its Chinese workforce has grown from 500 to 28,000 in five years. According to Flextronics Asia-Pacific President Ash Bharwaj, “Our low-cost footprint is better than anyone else in the region.”
Contract suppliers manufacture for many buyers. They aim to secure the cheapest labor and supplies and to maximize economies of scale and efficiencies. Starting as little more than cheap assembly lines, they have gradually taken on a wider range of productive functions and responsibilities, including design, engineering and procurement. Many of them have also taken over the factories of the major brand names, buying them directly from their previous owners. Contract manufacturers have become global players—expanding global reach and moving en masse to low-cost production bases in developing countries. China already hosts the largest number of such plants in the world.
While contract manufacturers employ huge numbers of workers, they hire very few of them directly. They prefer to go through employment agencies, because outsourcing recruiting also reduces costs.
The third layer of the computer supply chain is made up of the manufacturers of single components such as resistors, inductors and capacitors. Most of these companies are based in Asia. For example, one Taiwanese company, which manufactures in China, is the biggest producer of microchip resistors in the world, with a production capacity of 18 billion resistors a month, accounting for 16% of the world market. Component manufacturers also use employment agencies to deal with recruitment.
Squeezing the supply chain Cutting costs in the supply chain is of great importance to big computer companies. It is a successful strategy: one report estimated that computer component prices were falling by 1% a week in 2002.
Dell has achieved massive cost cutting in its supply chain. According to the company’s website, “Dell’s goal was to squeeze 60% out of its procurement cycle and costs, but process savings were only part of the attraction … The savings from supplier consolidation could be worth ten times the process improvements.”
Dell has not been alone in cutting costs. Hewlett Packard, as part of its post-merger strategy, has slashed supply-chain costs to the tune of US$3.5 billion. IBM reports that in 2002 alone it managed to cut about US$5 billion from its supply chain though a range of initiatives, including outsourcing deals.
Cinnamon rolls and labor rightsThis cost-cutting culture is illustrated in an account in the Wall Street Journal Online: “[Michael Dell] once chastised a supplier for bringing cinnamon rolls to a meeting with Dell employees. Michael walked in and said, ‘Take those back and let’s knock the price off the next shipment of materials you bring in,’ recalls Jim Cano, a now-retired Dell manufacturing executive who attended the meeting. ‘We don’t need food. We want a better price.’”
The financial press tells the story of the cinnamon rolls to illustrate Michael Dell’s toughness and acumen; and it undoubtedly indicates the talents that have made Dell the hugely successful company it is today. But the consequences of tough negotiation with suppliers extend beyond depriving top executives of mid-morning snacks. Further down the supply chain, workers feel the effects of relentless cost cutting far more acutely; their low wages leave them on the edge of subsistence.
Labor rights are human rights derived from the Universal Declaration of Human Rights. All workers are entitled to have their labor rights upheld. The international community has given responsibility for setting labor standards to the UN’s International Labor Organization (ILO). The ILO has a tripartite structure of governments, employers and workers’ representatives, as well as technical expertise in all matters relating to the world of work. For these reasons, the ILO is the authoritative and legitimate source of international labor standards.
Labor standards are contained in over 180 ILO Conventions. None has been ratified by all countries and only a few have been ratified by many. However, four standards are binding, notwithstanding the failure of governments to implement them: freedom of association and the effective recognition of the right to collective bargaining; the elimination of all forms of forced or compulsory labor; the effective abolition of child labor and the elimination of discrimination in all forms of employment and cooperation. These four are identified as Core Labor Standards in the ILO Declaration on Fundamental Principles and Rights at Work:
Many companies, as well as trade unions and nongovernmental organizations (NGOs), also recognize other labor standards as key to decent conditions for workers. These include measures to address health and safety; payment of a living wage; regular employment and the outlawing of excessive work hours and harsh or inhumane treatment.
While PC manufacturers bear a responsibility for promoting labor standards for workers in their supply chain, the experiences of workers in the electronics sectors, as well as the manufacturers’ current policy and practice, suggest that these companies are not yet taking their responsibilities seriously. According to one organization that works closely with major companies on labor standards, the big brands are complacent on this issue. They believe that “because factories are clean, they don’t have to worry about labor standards.”
A nonprofit monitoring organization commented that “the situation in garments and footwear is still nowhere near perfect, but attention is certainly being paid to the issues. The truth is that the electronics sector is guilty of the same types of abuses, but labor practices in the industry have not been put under close scrutiny the way the garments and footwear sector have been.” Many companies find that there is a business case for improving supply-chain labor standards, because better working conditions reduce the risk of operating in some countries. The increasing interest of the financial press in working conditions in the electronics sector supports the need for companies to recognize the business significance of labor rights.
Codes of conduct and
supply-chain labor standards The Catholic Agency for Overseas Development (CAFOD) measured the codes of conduct of Dell, Hewlett Packard and IBM against the standards included in the Base Code of the Ethical Trading Initiative (ETI), a UK tripartite organization of companies, NGOs and unions of which CAFOD is a member, using the information stated by the companies themselves.
HP’s code is superior in several respects to those of Dell and IBM. First, its code is specifically aimed at suppliers, while Dell and IBM build provisions on suppliers into the company’s general business code, making it harder to discern their commitment to improving labor standards in the supply chain. Second, HP’s code is clearly based on Core Labor Standards and other ILO standards, whereas Dell’s and IBM’s are generally not. For example, HP’s code has specific provisions on freedom of association, child labor and harsh or inhumane treatment, which the other two codes do not have.
In some respects, Dell’s code is superior to IBM’s Business Conduct Guidelines in relation to supply-chain labor standards. For example, Dell’s code has a specific provision on forced labor and on avoiding collaboration with entities that break laws regulating wages or working hours. The IBM Guidelines have no parallel provisions.
Such variables aside, however, the codes of all three companies, including Hewlett Packard, are deficient. First, with a few exceptions, the codes emphasize compliance with local law rather than adherence to international labor standards. While local law is crucial, it is often not implemented properly—as, for example, with overtime regulations in China. In those circumstances, codes can be a crucial means to inform workers of their rights and thus help them to enforce them. Companies should ensure that they promote workers’ rights by enshrining them in their own code of conduct. Second, none of the codes provides unequivocal freedom of association. This is a serious weakness when so many workers in the sector are unable to assert their rights. Third, none of the codes includes a commitment to providing regular employment. This is also a significant omission given that many of the problems suffered by workers in the electronics sector relate to their temporary status.
Implementation of labor standards policy Implementation standards vary widely. Again, however, Hewlett Packard demonstrates a greater commitment to improving labor standards in the supply chain than the other two companies. It has integrated labor standards more fully into its procurement practices, provides for communication of ethical expectations to suppliers as well as simply stipulating them in the contract, has made greater progress in assessing suppliers’ labor practices and integrating labor standards into management of relationships with suppliers and states specifically that the code applies to secondary suppliers.
Both Dell and IBM have introduced programs to monitor supply-chain labor standards, indicating increasing commitment to this issue, with Dell’s monitoring program somewhat more advanced than that of IBM at present. However, there are serious weaknesses in the implementation programs of all the companies. First, no company expresses a commitment to working transparently with other stakeholders such as unions, local NGOs or any workers’ groups to ensure sustainable improvement of working conditions. Second, no company emphasizes that, for improvements to be sustainable, workers themselves must take the lead in the improvement process. There is also no meaningful commitment by companies to incorporate labor standards into core business practices, for example, to paying suppliers a price that will allow them to implement codes of conduct. As a result, ethical trade staffs are attempting to raise standards while the dynamics of the industry are driving prices down and undermining suppliers’ ability to establish decent working conditions.
CAFOD’s research shows that in any event, the companies are not meeting the commitments they do make to workers, often tolerating illegal practices.
In contrast with the reticence of Dell and IBM, in particular, to commit to responsibility for supply-chain labor standards, all three companies pride themselves on being ahead of the curve on environmental issues and other elements of corporate social responsibility. Dell, for example, has prohibited the export of its environmentally sensitive waste to developing countries, and prohibited its primary and secondary recycling suppliers to use this material as landfill. Dell, HP and IBM lead the sector in sustainability assessments, because of their activities in bridging the digital divide—making computers accessible to more areas of the community—and in environmental activities such as take-back and recycling. It is to be hoped that they will now bring the expertise they have developed in other non-financial issues to the implementation of labor standards.
Mexico: Just passing throughCAFOD and its partners conducted research in Mexico and China, interviewing workers, managers and others associated with the electronics sector, to learn about working conditions in the computer factories first hand.
Guadalajara has been dubbed the “Silicon Valley” of Mexico. Its numerous electronics factories make and assemble components for computers, mobile phones, disc drives, printers, CD players, digital cameras, washing machines and dishwashers, among other electronic products. From the mid-1970s, US and Japanese companies, including IBM, Hewlett Packard, Dell, Texas Instruments, Xerox and NEC, sourced more and more products in Mexico, attracted by its favorable investment conditions, cheap labor, and—for the US companies—the mere hop across the border to their Texan and Californian science parks. From the mid-1980s to the mid-1990s, exports from the Mexican electronics industry grew from US$18.25 million to over $60 billion, and the industry generated 28,603 jobs in 1996 alone. Investment peaked in 1997 and came crashing down when the technology market and demand for electronics products collapsed in 2001. More than 15,000 jobs were lost in the first half of 2001. Many electronics companies fled Mexico seeking the cheaper wages of China.
The wider impact of the electronics sector on the Mexican economy has been disappointing. The country’s successful export sector has failed to carry the rest of the economy along with it and Gross Domestic Product (GDP) growth has remained slow, sometimes even contracting. Some 45 million Mexicans remain poor and levels of inequality between rich and poor are widening. Very little value is added to electronics products in Mexico and linkages with the domestic economy are weak. The electronics factories are “maquilas”—plants where imported components are assembled for export. In the 1990s, 95% of electronics products manufactured in Mexico were exported to the United States, while 90% of the components used in this manufacturing and 85% of all components were imported from there in the same period.
The relationship between the big US brands and the electronics workers of Guadalajara is indirect and complex. Most electronics firms operating in Guadalajara are contract manufacturers, for example SCI, Flextronics, Jabil and Solectron, hired to assemble electronics goods. For example, Dell contracted manufacturing to Jabil for several years until 2001; and SCI manufactured Hewlett Packard products.
IBM is an exception to the general rule. Uniquely among the major brands, it has had its own manufacturing facility in Guadalajara since 1975, specializing in the assembly of desktop and laptop computers. The company has become one of Mexico’s main exporters and the largest in the state of Jalisco. In 1998, it assembled 800,000 computers there. Combined with the 400,000 manufactured for IBM by the contract manufacturer Acer in Ciudad Juarez, near the US border, these represented 55% of the company’s total laptop production worldwide. In 2000, its Mexican production represented around 60% of IBM’s worldwide laptop output.
Although IBM owns the factory, most manufacturing is contracted out. In the past, the company ran a tendering process, with contract manufacturers bidding for specific manufacturing processes. The winners rented factory space from IBM, which kept its focus on quality control and coordination in the plant. This allowed IBM to respond rapidly to changing needs—for example by closing down an unprofitable production line or shifting production to another product (and often to another contract manufacturer). In 2003, however, IBM announced that it would outsource its entire manufacturing operation in Guadalajara to one contract manufacturer, Sanmina SCI.
IBM pioneered the system of recruiting through employment agencies, which continues with SCI. There are currently around 7,000 workers in the IBM factory, of whom only 500 are directly employed by IBM or by SCI—generally managers, supervisors and secretarial staff. The remaining 6,500 are recruited by employment agencies. The consequence is that the brand manufacturers are shielded from workers’ concerns by two intervening layers: the contract manufacturer and the employment agency.
Low wages, extra hours and no unions Thousands of workers are employed on the assembly lines of Guadalajara’s electronics factories. Pay, though higher than that of workers in factories producing for the domestic market, is low—typically US$50-$100 a week at companies such as IBM and Jabil, and less in some factories. A worker must do excessive overtime to earn close to US$100. A basket of basic food, rent, transport and clothing for a family of four amounts to about five times the legal minimum wage, and electronics workers typically earn less than half of the cost of that basket, which amounts to US$250 a week if clothing, education and some discretionary income are added.
Also, hours are long. Workers spent far more than the legal maximum number of hours in factories, partly because overtime is compulsory, and partly because low hourly rates mean that they must work excessive hours to earn enough to live.
Electronics workers, the majority of them young women aged between 18 and 25, with few economic resources and many of them single mothers, tend to be vulnerable, prepared to accept poor conditions in the workplace because they must provide for their children. Their expectations for their own lives are often low. Sister Luz Elena Barrios Calleros of the Center for Reflection and Labor Action (CEREAL), which facilitated CAFOD’s research in Guadalajara, runs courses on self-esteem for workers because she believes that low self-esteem perpetuates poor working conditions:
“It’s terrible to say, but many workers feel that what they get is what they deserve. Their opinion of themselves is often very low. They think because they didn’t finish high school or get a degree that ending up in a maquiladora is an inevitability. The treatment they’re subjected to in the maquilas makes this situation much worse. They’re treated as if they were ignorant and stupid. They tell us they’re treated like animals, shouted and sworn at, sometimes even pushed around. It’s a fundamental worker’s right to be respected, however lowly the job they are doing.”
According to Juan Carlos Páez, CEREAL’s human rights coordinator, the companies exploit workers’ vulnerability. They know “they can push the conditions further and further down, progressively lowering pay, benefits and safety precautions, yet the women will hang on—because they have to. The company knows exactly how fragile the situation of these workers is, and they exploit that.”
Sylvia, 28, a single mother of two daughters, was involved in a dispute with IBM when the company attempted to reduce wages: “My supervisor told me to shut my mouth if I care about my two children. He said, ‘Think about how you’re going to provide for them if we sack you.’ This is how they threaten you.”
Central to the difficulty workers face in asserting their rights is the absence of effective unions in the electronics factories. As Juan Carlos Páez says: “Unions can’t even get a foothold in the electronics sector, they’re blocked out by the employment agencies. People need to be educated and trained so they can protect themselves against exploitative practices. The more they know their rights, the more they can defend their own human dignity.”
Factories are unrelenting in their efforts to anticipate and forestall collective action, even discouraging workers from talking with colleagues in a group. Lupe, 28, comments: “It’s very difficult to discuss things at work with other colleagues, to try and get anything organized. If we were ever found talking in a group the supervisors would threaten us with the idea of the plant being closed, ‘If you don’t reach the production targets then all this work will go China,’ they told us. ‘There they are better workers than you and they get less pay.’”
Discrimination in recruitingThe recruitment methods used by employment agencies show the lengths to which companies will go to ensure a pliant workforce: agencies screen out potential “troublemakers” by discriminatory and often humiliating recruitment practices. CAFOD has seen a list of reasons for refusing employment applicants used by three agencies that hire workers for the IBM production line. The list clearly shows discrimination against, among others, gay men and lesbians, pregnant women and anyone who might encourage workers to negotiate collectively for better conditions.
“Reasons for rejection” in the psychological interview include: “Has brought labor claims, homosexual, socially inadequate, does not agree with IBM policies, signs of lesbianism, more than two tattoos, doesn’t respect authority, conflictive person, belongs to a political party as an active member, not disposed to work overtime, father is a lawyer, has a qualification in law, worked for a lawyer, worked for a union, transvestite, has earrings, has long hair.”
“Reasons for rejection” in the socioeconomic interview include: “has friends who are drug dependent, has a brother who is a union inspector, was a leader in presenting a complaint before Conciliation and Arbitration Committee; uninterested in work because pregnant; has previously been in IBM and makes negative remarks about redundancy conditions.”
“Reasons for rejection due to health” include “pregnancy.” In addition, there is age discrimination: it’s very hard for anyone over 30 to get a job in an electronics factory. A common feature of the interview process for jobs in the electronics industry is a “health test,” usually including urine and blood tests. Pregnancy testing is the norm, with some employers explicit about the purpose of the test, while others are vague: it’s “to see if you have any illness.”
According to Lupe: “In the interview with Caspem, when I first went into IBM, they ran tests on me: they took X-rays and samples of urine and blood. They didn’t tell us what the tests were for, and we never saw the results. This seemed normal to me at the time—I didn’t know there was anything wrong with it. I mean, I assumed of course that they didn’t want people with any illnesses, or women who were pregnant, because they don’t want to pay for any time off. But until I met CEREAL, I didn’t realize these were violations of our rights.”
A totally humiliating experienceWomen workers interviewed by CAFOD told how they were examined naked and asked intrusive personal questions such as, “Do you have a boyfriend?” “How often do you have sex?” and “Do you have children?” Jannet, 20, reported: “I had to fill in a questionnaire; it had some really personal questions in it. They asked, ‘How many boyfriends have you had? When did you last have sex? How many times? Do you have any sexually transmitted diseases?’ I stopped filling in the answers.”
The agencies also visit potential recruits in their home, examine their possessions and interview their neighbors. Workers told CAFOD that their families and neighbors had been asked who their friends and associates were, whether they kept good company and if they have a drinking or drug problem.
According to Ramona, 24: “They came round to the house and spent half an hour looking around at our possessions. I suppose they don’t want too big a gap between how you live and your conditions in the factory. They talk to your neighbors, to find out what sort of friends you have.”
Contract manufacturer SCI recruited Monica, 26, to work on an assembly line making Hewlett Packard printers in 1999; she worked on the HP line until 2001: “They did a psychometric test on me and then asked normal questions, without all the personal stuff I had at IBM. But then came the medical exam. I was in a room with two nurses; well, they were dressed like nurses anyway. They were both very rude and really bullied me around, shouting at me to do this, do that. They asked me all these questions about drinking, smoking, illnesses in the family. Then one said, ‘Strip off, I need to check you for tattoos.’ My word wasn’t good enough. I had to take off all my clothes, including my underwear. They even touched me while I was naked, checking my breasts. I don’t know what they were really looking for.
“After that, they asked me if I was pregnant. I said no, but that wasn’t enough. They gave me a test paper and ordered me into the bathroom telling me to do the pregnancy test. They said, ‘“If you have your period then you have to show us your sanitary towel to prove that you are bleeding.’ It was a totally humiliating experience, the worst thing I’ve ever had to go through. It was completely degrading. But I didn’t know how to complain—I mean, they were doing the same thing to everyone.” CAFOD has anecdotal evidence from many other workers that these practices continue.
Recruitment agencies and workers’ rights Mexican labor law requires that employment agencies must provide exactly the same conditions as the ultimate employer. However, agencies avoid this provision by registering themselves as “manufacturing sub-contractors.” The agency then employs workers on significantly worse terms than those of direct employees of the company, cutting employment costs by 10% to 40%. This system has serious negative consequences for workers.
Short-term contracts. According to CEREAL’s Juan Carlos Páez, “about 90% of the workers who come to us for help are from the electronics sector. This is partly due to the sector’s instability, with all the hiring and firing that goes on as big orders, or even entire companies, come and go. Of all the sectors we work with, electronics is the most volatile, and this leads to many violations of people’s rights. The modus operandi of the electronics sector is what we call ‘seagull capital’—it alights here in Mexico for a little while, then flies off to China or Taiwan.”
The jobs of workers employed by agencies are constantly under threat. Workers are employed on consecutive short-term contracts of between 28 days and three months, and remain on such contracts sometimes for several years, although Mexican law bans this practice. Short contracts make it easier to “hire and fire.” If there’s a dip in demand, workers can simply be dismissed when their contracts expire. As a result, workers live in an atmosphere of constant insecurity and fear. One worker who was employed by three different agencies while working in the IBM factory said, “You never feel secure in that environment… Uncertainty is a permanent factor; you never know whether you’ll be working next week.” There’s no unemployment benefit in Mexico, and losing one’s job can mean an abrupt fall into poverty. According to CEREAL, “If you don’t earn, you don’t eat.”
Short-term contracts are particularly harmful to women, because they are used as a mechanism to avoid paying maternity benefits: when a woman becomes pregnant, her contract is simply not renewed. One worker, when asked what single change would improve her life immediately said: “Permanent contracts!”
Denial of benefits. Employment through agencies is also a means of paying workers fewer benefits. Those sacked after a string of short-term contracts do not receive the “length of service” payment to which workers are entitled on termination of direct employment.
Lupe, 28, used to work in the IBM factory. “In June 2001, IBM tried to lower all our salaries across the different agencies. Oscar [from CEREAL] left slips of paper in our lockers saying there was going to be a meeting. We had already decided individually that we weren’t going to accept the cut, so 50 of us went. It really hit me, hearing about my human rights and labor rights for the first time. It was the first I knew about all the benefits we were losing through having the one-month contracts. I thought to myself, the employers are doing exactly as they like and we don’t even know it’s wrong! I just couldn’t believe how the agencies were robbing us. CEREAL took us to see the press, we went all over the place. And we won! After the press attention, they decided not to cut our salaries. I felt so good, so satisfied when we won. Articles were published saying that because we had resisted, we had managed to beat IBM. Because of the problems we had, we ended up learning about all our other rights, not just about salaries. If I hadn’t known all this, I would have accepted the tiny payoff Caspem [the employment agency] tried to give me.
Redundancy pay. This account is from someone who worked on a conveyor belt assembling hard drives in the IBM factory and was fired in July 2003 by an employment agency after asking to be put on a permanent contract: “The director called me in when I started asking for my rights, after I’d spoken to CEREAL. She said, ‘I want to know who’s giving you advice. It’s obvious that someone is helping you, from the way you talk.’ I denied it. She was pushy and aggressive, treating me as if I were completely ignorant. She said, ‘If I want to I can sack you right now without giving you a cent.’ But I wasn’t afraid of her. I never got what I asked for; they sacked me instead, but I was already prepared so at my first redundancy interview I went through the payment details they showed me line by line. It was full of errors, showing that I was owed less than I really was. I told them to correct the errors.
When I came back the next day, I took along a page of calculations we had prepared at CEREAL, showing the liquidation payment I was due. I said, ‘This is my proposal. I know what I’m legally owed.’ She offered me 13,000 pesos [US$1,300] but I was owed 18,000. They went up to 15,000 but I was still not satisfied, and I went to the Conciliation and Arbitration Committee, but they gave me no help at all. I arrived with a lawyer, a friend of mine. ‘Personal lawyers are not permitted,’ they said. ‘We’ll provide you with one.’ Of course, the lawyer they gave me was on the company’s side. They offered the 15,000 again and said, ‘You’d better take it because it’s all you’re getting.’ So in the end I accepted it.”
Vacation rights. Many social security payments in Mexico are dependent on continuous length of service, so workers with many periods of short employment find it difficult to acquire the right to a pension or to housing benefits. Short-term contracts also force workers to forego holidays: Mexican workers must work a year’s permanent contract to earn six days’ holiday and time off does not accrue at all on monthly contracts. Ramona, who is 24, describes the effects of this system when she worked in IBM’s factory: “They even refused to give me any time off work when my dad died. The law says we should get three days’ compassionate leave. They said I couldn’t even take it as part of my holiday entitlement. I obviously had to go, so I paid someone to do one of my days, then I just took the other two anyway to go to the funeral. The personnel officer deducted two days off my pay.”
Fired for talking to CAFODCAFOD conducted its research in Guadalajara in April 2003. Days after having talked to us, three workers—Ramona, Lupe and one man—were fired. Ramona is unmarried and has no children. She lives with her mother, whom she supports, in a well-established neighborhood where many houses were built by the state for sale to low-income families. When she was fired, she had been working at IBM for four years, employed by agencies on one-month contracts throughout.
“I had the talk with CAFOD on Wednesday. Nine days later, on the Friday, I was sacked. With the pretext that I had arrived late to work, they told me to change out of my work clothes and go to personnel. As soon as they told me this, I knew I was being fired.
“I was taken from the factory in a car to the Caspem offices. On the way, they questioned me about whether Lupe was a good friend of mine. I wasn’t sure yet why I was going to be sacked. I thought it might be because I had been there long enough and they didn’t want me to accumulate length of service—they don’t like you to work there for too long even on the one-month contracts. Or it could have been because they thought I was difficult, because I didn’t like the way I got pushed around.
“But when I got to the office the personnel woman said straight away: ‘Did you know those English people who were talking to you?’ And she asked me who my lawyer was. She said a rumor had reached her that I was leaking information about the company. I said I didn’t know them and that I had just met them in the street. She accused me of being a ringleader and threatened to blacklist me. She then put up a show that she wasn’t sacking me for this but because of my length of service—basically they tell you that you’ve been there for four years or however long it is, and therefore your time is up, as if this made any sense. She offered me a check for 2,000 pesos [US$200]. I said I was owed 12,000. They try to force you to sign while you are still in there, so you don’t have time to go ask anyone for advice about whether the amount they offer is right. Eventually she gave me 11,000, which wasn’t bad. I think they wanted to pay us off and shut us up quickly because they could see we had outside contacts helping us.
“In one way, I wasn’t too sad to leave that place because the atmosphere was always so tense. The supervisors were very difficult and we weren’t allowed to talk to each other during the day. The people directly contracted by IBM then were much better off—although there aren’t many of them, only one per line. They get paid holidays and a two-day outing at Christmas for all the family, paid for by the company. They get canteen coupons, production bonuses, savings funds, medical insurance.” Ramona now works at another electronics factory, making mobile telephones.
The treatment of these workers in factories supplying major computer companies is a vivid example of the degradation of the workers employed on electronics assembly lines. The swift action by labor contractors in ridding themselves of dissenters shows that they know their treatment of workers is unacceptable. As Ramona says: “It’s obvious from their questions that they have something to hide and don’t want anyone in authority to find out.”
Subcontracting in ThailandThailand is the world’s second largest producer of hard disk drives (HDDs). The industry grew up on the back of large-scale investments from computer multinationals attracted by low labor costs. In recent years, however, prices for HDDs have fallen and low-wage competition from China has been intense. HDD industry wages in China are estimated to be 50% of those in Thailand. The average price per megabyte for an HDD was US$11.54 in 1998; in 2002 the price hovered between US$0.05 and US$0.15. In response, companies operating in Thailand have been cutting costs by using subcontracted labor.
CAFOD interviewed subcontracted workers in the Thai HDD industry, who clearly have a rougher deal than their directly employed colleagues. Many are younger and they look tired, with old, dirty clothes rather than uniforms. The workers we spoke to were paid around half the wage of permanently contracted workers—about US$4.25 a day. This is the legal minimum wage, but it does not cover a Thai household’s average monthly expenditure on food and housing.
If subcontracted workers fall ill, they do not receive sick pay or social security payments, nor (in contravention of Thai labor law) do they receive any paid annual leave or paid leave on public holidays. The overtime pay they receive does not meet legal requirements for direct employees, so they are asked to do most of the overtime. Subcontracted workers to whom CAFOD spoke have to work overtime of “sometimes four hours a day, sometimes eight hours.” Like their Mexican counterparts, subcontracted workers in Thailand are dismissed if they become pregnant.
China: The world’s mega-computer factoryChina is now the largest developing country exporter, the world’s largest recipient of foreign direct investment (FDI) and the fourth-largest industrial producer behind the US, Japan and Germany. Its export growth has been tremendous, reverberating in markets throughout the world. In 2002, China accounted for 60% of world export growth, and in the last 20 years has emerged as the world’s leading electronics manufacturing location. While electronics factories elsewhere in Asia have been suffering, many plants in China are reportedly doubling output in 2003. In 1999-2000, China’s two top export products were telecommunications equipment and computers. In 2000, high technology products accounted for 22% of China’s total exports. In the same year, 25 out of 30 of the largest foreign transnationals to export from China were electronics or telecommunications companies.
China is becoming a “global factory” for the computer industry. Huge factory complexes, many funded by Taiwanese capital, produce the components and parts for the global electronics industry. These factories are involved in many parts of component manufacture and assembly: factories in the Pearl River Delta region produce CD and DVD ROMs, scanners, keyboards, monitors, desktop and laptop PCs, passive components (such as capacitors and resistors), printed circuit boards, power supplies and mobile phones.
Chinese success is based largely on low wages. China’s wages are a fraction of those of its main competitors—half the rate of Indonesia’s, a quarter that of Malaysia and the Philippines, an eighth of Mexico’s and around 5% of Taiwan’s manufacturing wage. Hourly manufacturing wages average US$0.60, for a labor force based on a massive pool of migrant workers from rural China.
While electronics production is concentrated in the Pearl Delta region, the workers in Chinese factories are mostly migrants from further north, often young women who seek a job in an export factory to save money to send home. Typically, workers are recruited through labor agents and vocational schools in inland provinces.
Most live in cramped conditions in dormitories on the factory site. Typically, around 10 to 15 people sleep on bunk beds in each dormitory. The dormitories vary widely in standards. Some are acceptable to workers, while others are dirty, inadequately heated and ventilated and without hot water or sufficient washing facilities, so that workers have to stand in long lines to shower after an 11-hour shift. Workers generally eat all their meals in the factory, with some providing adequate food while in others workers complain that the food is poor.
Obligatory excessive overtime and low wages Very long, compulsory overtime and wages below the legal minimum are endemic in Chinese factories, and the electronics sector is no exception. According to Chinese labor law, workers are entitled to at least one day off a week and overtime should not exceed 3 hours a day or 36 hours a month. The legal minimum wage in Dongguan, where most of CAFOD’s research was done, was around US$54 a month in 2002, calculated based on an eight-hour working day. Workers should thus not be expected to work overtime to earn it. The law also requires weekday overtime to be paid at 150% of the regular daily rate, Saturday and Sunday overtime at 200% and overtime on a statutory holiday at 300%. However, the Chinese labor authorities do not enforce the law, partly because of their weak capacity; their staff is under-resourced and lacks appropriate training.
Workers in the electronics factories that supply major brands routinely work hours far in excess of the legal maximum and without receiving the overtime stipulated in the law. One Taiwanese company with five factories in Dongguan City supplies many different components to major computer brands. During the peak season, assembly workers in these factories work 3 to 5 hours of overtime a day, an average of 100 to 120 hours a month and 7 days a week. In the slack season, workers are given days off, but without pay. These working hours are typical, although hours can be even longer in other factories: up to 15 or 16 a day in the peak season. Some workers work all night in peak periods.
Wages in these factories are well below the minimum of US$54 a month, with the basic wage US$37 (increasing to US$39 after working for one year and to US$42 after two years). To earn the minimum wage, workers must do illegal amounts of overtime. They may earn as little as US$36 in the low season. Although workers receive up to US$72 during the peak season, they can only earn this by working unacceptable amounts of overtime.
Miss C, aged 20, told us: “Everything in this factory looks nice. The only thing is the low wages. I’ve been in the factory for two years and the highest income I ever got is a little more than 500 renminbi ($60), after having worked more than 100 overtime hours.… How can that money be enough for us? At least you have to buy everyday provisions, and if I buy some clothing for myself, my income is finished. It’s even worse in the low season when we have no overtime work. Our basic wage is deducted when we’re forced to have a day off because no order is placed and we have no work to do. I don’t find it too harsh working here. The only thing is low wages. We all want to earn more.”
These excessive working hours do not boost factory profits. Recent research suggests that there is a business case for reducing overtime at supplier factories in China: cutting hours can help increase productivity. Many factories operate at 35% to 75% of their capacity and there is a clear link between high levels of overtime and low productivity. A cultural change is needed to make shorter working hours acceptable.
Indebted even before starting to workWages are often reduced further by the need to pay debts to labor agencies that charge a high fee to place workers in jobs. Often factories retain wages so that workers receive them some weeks after they are due. Workers who resign do not receive the backdated wages owed them. To prevent workers from quitting in the peak season, one factory deducts about 10% of workers’ wages in the first year of employment, returning the money after 12 months. Many workers have no written contract, so cannot hold management to account for payment of proper overtime rates and hours. In peak seasons, workers cannot even take sick leave: if they take a day off, wages are deducted.
Miss A is 18 and has been working in an electronics factory since she was 16. She finished junior high school at home in Shanxi province. When she learned that factories in Guangdong province were recruiting new workers, she went to a local labor agency to register. She paid the agency 750 renminbi ($91) and they arranged a place for her on a coach carrying young women workers from Shanxi to a factory in Dongguan City. She then paid the factory 50 renminbi ($6) as down payment for her job. In the end, she was $121 in debt before starting work. At first, she thought she would be able to return the money soon after entering the factory, but she was disappointed. In the first six months, she received the equivalent of only $36-48 a month, and after buying food and other daily provisions, had nothing left.
Physical and psychological pressureFactories have harsh penalty systems and exert strong psychological pressure over workers. In one factory, US$0.25 US cents are deducted from wages if a worker violates a factory or dormitory rule. In another, US$0.06 cents are deducted for each minute a worker is late. If workers are absent without permission, US$3 is deducted. Workers are allowed to leave the factory premises only on Wednesdays, Saturdays and Sundays; at other times, they must obtain permission. Elsewhere, workers are forbidden to talk during work, and are fined for not sitting properly. In one factory, a worker is fined US$3.60 for her first mistake in production and twice that for a second. In one plant, which makes monitors, managers have the right to fire workers who step on the grass in the factory complex. In another, workers caught littering must wear a placard saying, “I am a garbage producer.”
The need to deliver quality products on time often means that workers are under great pressure not to make mistakes and to achieve production quotas, which are set by the day or by the hour. Conveyor belts are sometimes speeded up when there is a rush to deliver on time. In one keyboard factory, the job of each worker on a conveyor belt is to insert six or seven keys into the board. Each worker must finish 300 keyboards an hour, which means inserting each set of six or seven keys and moving on to the next within 12 seconds, and continue to do so for 12 hours. Workers testing monitors must test 150 an hour—24 seconds per monitor.
Workers live in fear of criticism from supervisors and feel under intense psychological pressure. In a factory that makes components for laptop computers, workers are not allowed to talk, stretch or look around, and may not leave the production line to use the toilet or drink water. In a factory making monitors, a worker who makes a mistake must wear a red overcoat. Workers interviewed for this research consistently complain of finding the work extremely stressful: many say they have nightmares about being criticized and penalized at work.
Health, safety and insuranceUnder Chinese labor law, employers must pay for workers’ retirement and industrial injury insurance, but in many electronics factories workers are not covered by one or both of these types of insurance. Sometimes only those working in a particularly risky activity are insured for industrial injury, or only senior staff—supervisors and above—have retirement insurance.
Most people assume that electronics factories are at least clean, because of the precision required in manufacturing computers, but a clean factory is not necessarily a safe factory and many electronics workers operate in a dangerous or unhealthy environment. Many factories have no health and safety department, and fail to provide workers with health and safety training.
Some workers are exposed to dangerous chemicals, such as the solvents used to clean parts such as computer cases and the liquid and powder paints with which they are then sprayed. Because the chemicals are usually supplied in unlabelled containers and the workers are not given chemical safety training, much less appropriate protection, workers rarely know the names of the chemicals they are using, whether they are dangerous and what protection they should use. In one factory, workers dealing with solvents are given cotton gloves, to protect the components from the workers’ sweat more than to protect the workers’ hands. The workers don’t wear the gloves because they slow themup, making it harder to achieve production quotas and are ineffective in any event; they become soaked through with solvents so many workers get rashes and spots on their hands even when wearing them.
Workers who solder components onto metal boards are exposed to smoke and complain of skin irritation and breathing difficulties. Those making printed circuit boards suffer from chemicals most: their job is to dip the board into different chemicals that of course come in contact with their skin. They often suffer from rashes. Chemicals are also not properly stored. One worker joked that the factory looked more like a petrochemical plant than an electronics factory.
In December 2001, there was a fire in a factory that makes computer cases and peripherals. A machine used to mold computer cases had had an oil spill and the workers on duty, who had not received health and safety training, used a flammable thinner to clean the floor. When the thinner caught fire, eight workers were burnt, two over 30% of their body, including their faces and feet, and they now have difficulty walking. Another has difficulty using her hands. The workers in the factory were not insured for industrial accidents at that time and those injured have not been compensated according to the law. The factory had no fire drill or fire safety training.
Chemicals are not the only hazard. In some factories, workers are subjected to noise pollution because the machines that press components together are very loud. Workers are given cotton earplugs every six months, but they last only two weeks. In one factory that makes components, the grinding department grinds up metal debris, creating a great deal of metal dust. The workers do not wear protective masks. They develop dry sore throats and hoarse voices. Workers on production lines often find that their legs, backs and shoulders become stiff and sore after standing at work for up to 11 hours. Those who test monitors sit in front of them for up to 11 hours a day, looking at a flashing screen. They often have eye problems, including tired and swollen eyes, and after a while, their vision becomes blurred. The factory gives them no education about eye problems that might arise from their work. Others, whose job is to insert components into boards, work through microscopes all day. Their eyes, too, become tired, swollen and dry. These problems are exacerbated because workers feel that they cannot lift their heads to look around occasionally.
One Chinese worker told us, “Our two hands are working every minute and so are our brains. Our hands must move as fast as our brain. If you lose your concentration for even a second, you produce a defective product. They subtract points and your production bonus is sure to be reduced at the end of the month.” This pressure is exhausting, and only worsened by the Chinese manager of one electronics plant who described his solution to health problems this way: “China is full of girls with pretty eyes and strong hands. If we end up without people, we just look for more.”
But bad practice is avoidable. Workers interviewed in one factory that assembles mice and digital cameras praised its health and safety management. Their workplace is air-conditioned, cooling both machines and air temperature; workers can sit while they work; there are short breaks between work sessions; there is good ventilation which captures the chemical-laden smoke that soldering produces; and workers are provided with gloves and masks.
A country without real unionsThe problems experienced by Chinese workers are closely linked to their inability to bargain collectively to improve working conditions. Chinese workers are not represented by free, democratic trade unions. There is only one legal union, the state-controlled All China Federation of Trade Unions (ACFTU), which is not recognized by international trade union federations. Lack of representative organizations affects workers in the electronics sector as it does all other Chinese workers, making it very hard for them to assert their rights and achieve sustainable improvements in working conditions.
Nor do workers generally participate in factory decision-making in any other way: very few electronics factories consult workers on any aspect of their work, and few factory health and safety committees have worker representatives. Managers clamp down on any show of solidarity by workers. One factory, which assembles monitors, has a rule that workers who “gather together illegally and disturb production” are dismissed. The absence of effective unions or other collective action is reflected in workers’ low awareness of their rights under Chinese law. In one factory making keyboards, not one worker interviewed knew about Chinese labor laws.
CAFOD’s research on working conditions in Chinese electronics factories was conducted by the Hong Kong Christian Industrial Committee (HKCIC), which does educational and advocacy activities on workers’ rights and promotes the independent trade union movement. It is not easy for NGOs to obtain access to Chinese electronics factories and is particularly hard to have candid conversations with workers.
Agenda for changeWorkers in the electronics sector are getting a raw deal. Political will is lacking at both the international and national level, while companies lack commitment to labor rights and are reluctant to intervene in supply-chain operations that enable them to cut costs. All this combines with lack of awareness by northern consumers, and above all the undermining of workers’ ability to speak out on their own behalf to drive working conditions down.
The strategy of outsourcing to low-wage countries is not intrinsically bad for workers, but the distribution of benefits in the electronics sector is currently weighted too far in favor of northern transnational corporations and consumers. It needs to be rebalanced in favor of the poor. That requires a series of fair labor practices by the transnational computer manufacturers and institutional investors, enforcement by host governments, monitoring by trade unions and international union federations, advocacy by the international community and market pressure from individual and institutional consumers.
The Catholic Agency for Overseas Development (CAFOD) is the English and Welsh arm of Caritas International, a worldwide network of Catholic relief and development organizations. It is a founding member of the Ethical Trading Initiative, a tripartite organization of UK and global retailers, trade unions and NGOs working together to improve supply-chain labor standards through the implementation of the ETI Base Code, an agreed-upon code of conduct based on ILO standards. For more information on ETI, visit www.ethicaltrade.org and to learn more about CAFOD, which has been fighting third world poverty since 1962, visit www.cafod.org.uk. This report was prepared by Catherine Astill and Matthew Griffith, and summarized by envío.
|